CO2 Booster Systems Explained
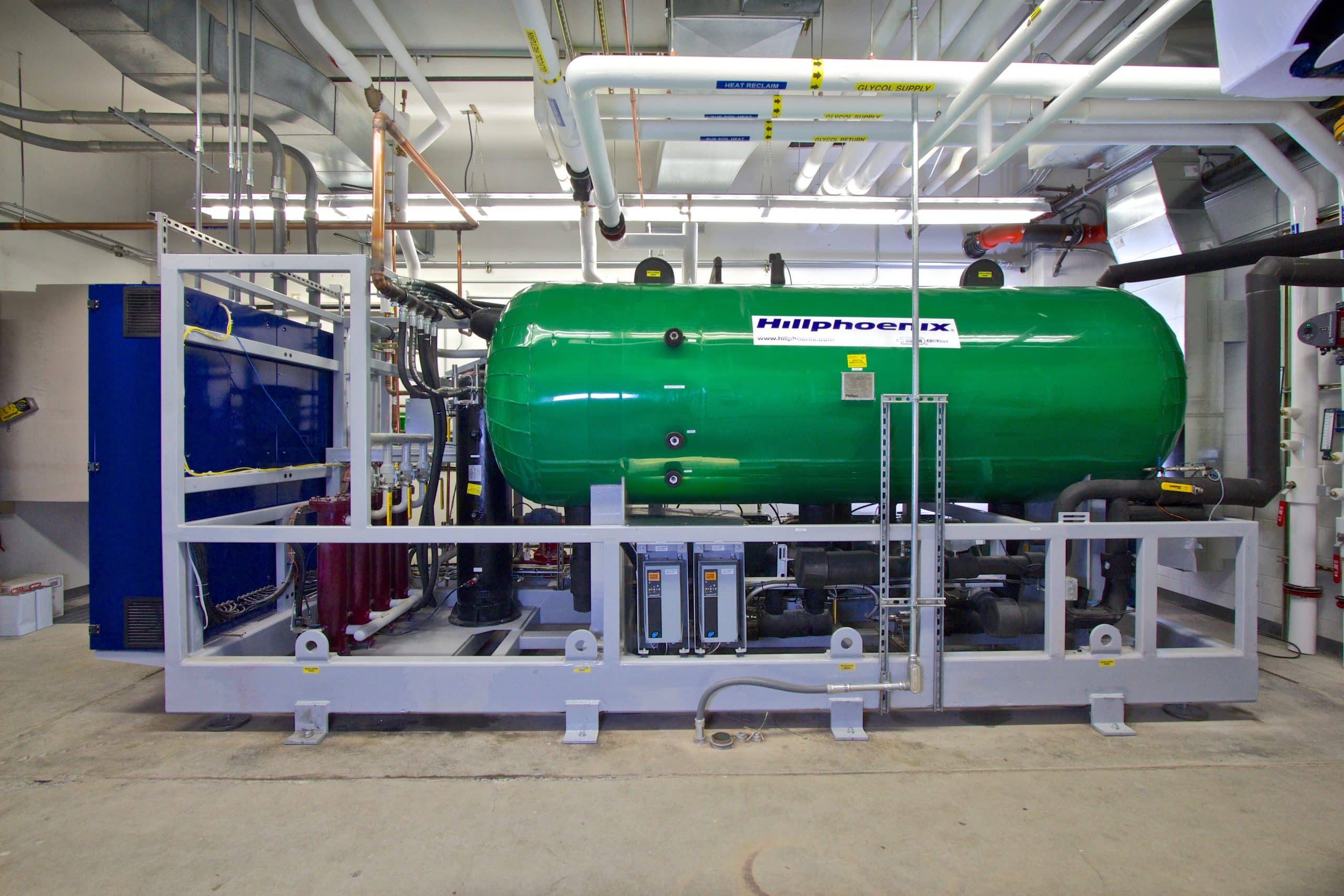
Advances in technology have made the use of environmentally friendly CO2 refrigerant in booster systems practical across a wide range of applications. Since early this decade, supermarkets in North America have increasingly been coming to rely on these systems. Industrial operators are also beginning to appreciate their advantages. But not everyone understands how they work.
Since the middle of the last decade, CO2 has been used as a refrigerant in both secondary and cascade-type systems across the grocery and supermarket industry. These approaches rely on CO2 as either a single-phase secondary coolant, or as a lower cascade direct expansion refrigerant. In either case, the systems use CO2 in combination with another refrigerant, typically one of the commonly used HFC refrigerants that are less environmentally friendly than CO2.
But a booster system uses only CO2. It is able to do so without having to rely on any HFC refrigerants because of in part the function of two main components that are not found on traditional types of systems: a high-pressure control valve and a flash-gas bypass valve.
In order to achieve a higher level of efficiency, CO2 booster systems must be able to operate at greater pressures that are needed for other commonly used refrigerants. These systems, in other words, operate under certain conditions beyond the critical point of CO2 which occurs at 88°F and 1055 psig. In fact, discharge pressure can reach as much as 1450 psig. These special components are needed so that the system can still operate efficiently at these pressures.
A third component that is necessary for the operation of the system, but that most of the time works as a condenser like the ones on most other types of systems is called condenser/gas cooler. When the ambient conditions rise above 80°F and the system begins running in the supercritical range of CO2, the discharge gas leaving the compressors is unable to undergo any further state change. It instead remains a supercritical gas, or fluid, as it is also called.
This supercritical gas exits the condenser/gas cooler and flows to the first of the special components mentioned above, the high-pressure control valve. From the valve, the CO2 expands into an intermediate pressure receiver called a flash tank. The valve works somewhat like a holdback valve during transcritical operation (above 88°F ambient) in order to maintain optimum pressure through the gas cooler for the most efficient operation of the system in this state.
The expanded gas leaving the high-pressure control valve flows into the flash tank at around 540 psig. The flash tank performs the same function as that of a receiver on a conventional system. But on a booster system, the flash tank is equipped with the second special component, a flash gas bypass valve, that sends vapor from the tank to the medium-temperature suction header where it joins the gas from the medium-temperature evaporators returning to the medium-temperature compressors. Doing this maintains operational pressure in the flash tank.
It is because of these components that CO2 booster systems have become a practical alternative to traditional systems for almost any type of application, from c-stores to supermarkets to ice rinks and other industrial operations.