Debunking the Myths Around CO2 Refrigeration Systems
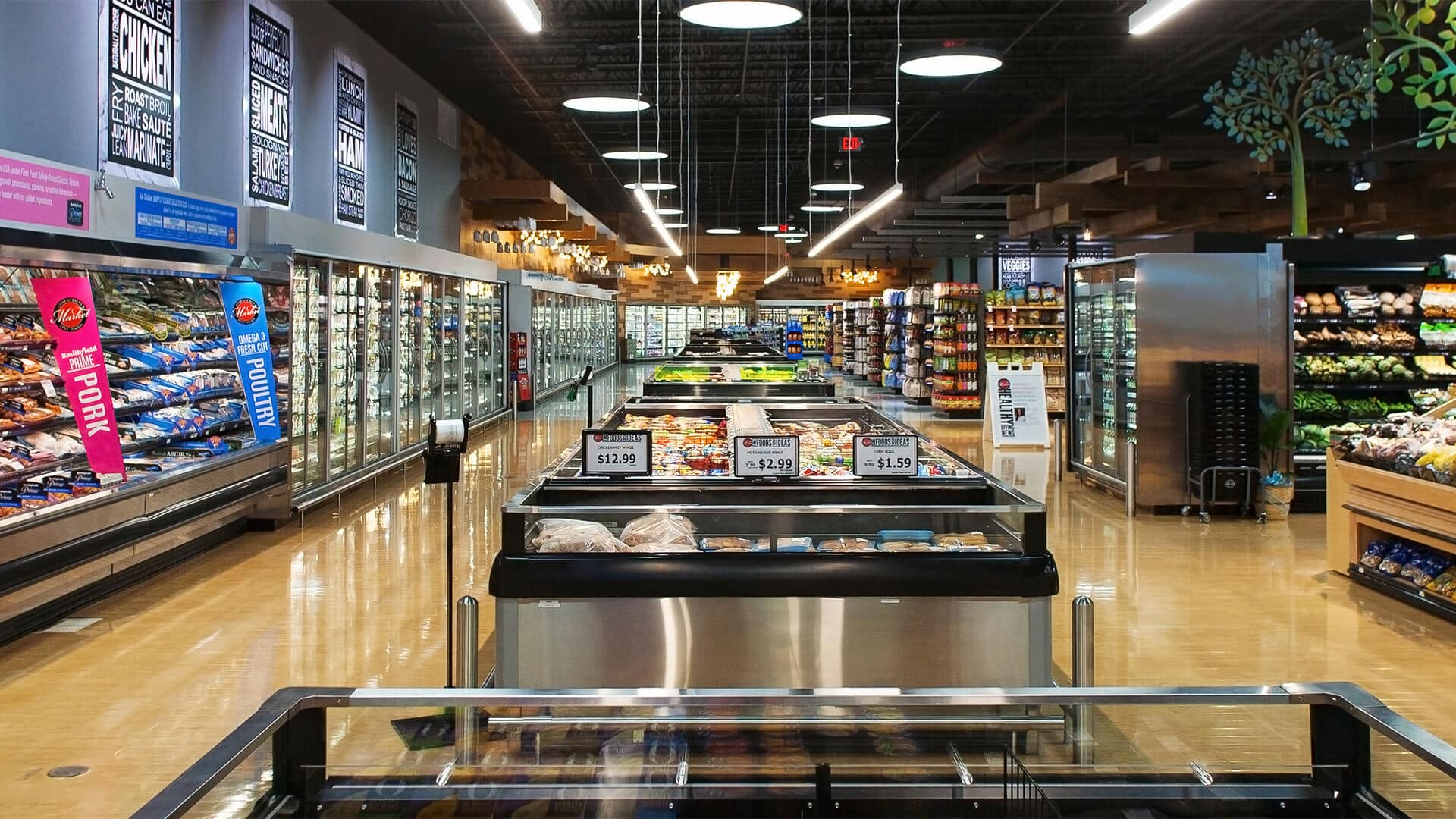
Carbon dioxide (CO2) has been used as a safe and reliable refrigerant since the Industrial Revolution. Now, modern food retailers are adopting CO2 as their preferred refrigerant – and for good reason. The list of advantages using CO2 is comprehensive:
- It is a natural refrigerant
- It is an odorless, non-corrosive, non-toxic and non-flammable Class A1 refrigerant
- It has no ozone depletion potential (ODP) and with a global warming potential (GWP) of 1, it is the basis by which all other refrigerants are measured
- It offers significant energy and operational cost savings
- It has low service and maintenance costs since it can be vented to the atmosphere and does not have to be captured or reclaimed
- It doesn’t run afoul of regulatory issues and you won’t be subject to fines or penalties
Background on CFCs vs. HFCs vs. CO2
The first major example of competition with CO2 refrigerants came in the 1930s, with the creation of “synthetic refrigerants” called chlorofluorocarbons (CFCs). CFCs eventually gave way to hydrofluorocarbon (HFC) refrigerants, and HFCs were considered more stable and more reliable in the higher ambient temperatures below the so-called “CO2 Equator.”
CO2 started to be seen as a secondary refrigerant. However, a series of technological innovations – coupled with the harmful effects HFCs have on the environment – helped restore CO2’s standing as a scalable, sustainable refrigerant.
However, that hasn’t stopped the spread of misinformation about CO2.
Myth 1: You Can’t Use Transcritical CO2 Below the CO2 Equator
Because ambient temperatures get higher the closer you get to the equator, a misguided argument was created that you shouldn’t use transcritical CO2 systems below the so-called “CO2 Equator.” Instead, it was believed you should use a subcritical CO2 system – or one in which the refrigerant can be condensed.
Around 10 years ago, whispers began that the “CO2 Equator” was disappearing. Those whispers became shouts after a series of technological advances:
- Adiabatic Gas Coolers: Combines the condensing of the refrigerant with the adiabatic cooling of the air
- High-Pressure Sub-Coolers: Uses a small mechanical vapor-compression cycle coupled to the main cycle at the exit point of the condenser to provide sub-cooling
- Parallel Compression Systems: Compresses excess (flash) gas at the highest pressure level possible to improve overall energy efficiency
- Gas Ejector Systems: Recovers the energy of the high-pressure side of the system to reduce the work required on the lower-pressure side of the system
The Reality
The “CO2 Equator” myth is no longer relevant, thanks to advances in refrigeration system technology. Even if there ever was any truth to it, those days are long gone.
Myth 2: CO2 Requires Significantly More Energy vs. Traditional Refrigerants
Perception is reality with this myth, but a side-by-side comparison between a system featuring an R449A refrigerant, which is a blend of hydrofluoroolefins (HFOs) and hydrofluorocarbons (HFCs), and one with R744 (CO2) refrigerant helps reveal why this is false.
In this case, there’s an important engineering difference, and side-by-side tests in seven U.S. cities (Minneapolis, Sacramento, St. Louis, New York, Seattle, Atlanta, and Miami) help illustrate this difference.
Many operators will mistakenly size their CO2 system according to HFC-system parameters, but the inherent differences in the two types of systems mean an improperly designed CO2 system can be 17% (in Seattle) to 22% (Miami) less efficient than an R449A system.
However, when you properly design the CO2 system and add components – adiabatic gas coolers, parallel compressors, parallel compressors with high-pressure ejectors and electronic expansion valves (EEVs) – the reality is a CO2 system can be more efficient than the R449A system.
The Reality
There are many energy-saving possibilities when you use CO2 refrigerant in a properly designed system, many of which are compounded when you add other components like adiabatic gas coolers, parallel compressors and EEVs.
Myth 3: There’s a Huge Increase in Energy Consumption When the CO2 System Goes Supercritical
As the subcritical ambient temperature (less than 87ºF) around the refrigerant system moves toward the supercritical CO2 temperature of 87ºF, the belief was that there would be a significant and immediate spike in energy usage when subcritical/supercritical line was crossed.
This made stores nervous, especially in warmer climates. But in actuality, there is no so-called spike.
The Reality
While kilowatt (kW) usage does increase as the supercritical temperature threshold is passed, no drastic spike is experienced.
Energy consumption increases along the same steady path as it does in subcritical temperatures – just like any other refrigerant.
Myth 4: CO2 Refrigerant Systems Are Too Complex
This myth may have persisted because a schematic drawing of a typical system does feature several valves (high-pressure, electronic expansion and flash-gas bypass), transcritical and subcritical compressors, case and rack controllers, coolers, condensers and heat-reclaim systems.
That can sound like a lot to keep track of.
However, advances in technology have also busted this myth. The key innovation here is electronic expansion valves (EEVs), which are much easier to work with than mechanical valves.
Also, CO2 refrigerant systems can now be controlled and optimized by computers. Every system function is read through transducers, temperature sensors and analog and digital inputs. Operation is reported/recorded via electronic software and hardware.
Now an effective computer-controlled system is all you need to ensure proper operation. That eliminates the need for a technician to constantly monitor and manually adjust the system’s valves and other components.
The Reality
While the design and components of CO2 refrigerant systems are similar to those used for many years, electronically controlled components make them more reliable and give them longer service life – resulting in a decidedly less complex and more robust system.
Myth 5: Pressure in a CO2 System Is Dangerously High
Pressure is required to operate a CO2 system, and some people fear the pressure that may exist on a hot summer day – up to 1,600 psi – is dangerous to anyone who comes into close contact with the coolers or freezers. Some critics go as far as saying the system’s pressure can be a serious risk to shoppers on the floor.
The truth? All sections of the CO2 system that require high pressure are located either in an equipment room or on the roof – posing no risk to shoppers or employees.
Another way to debunk this myth is by looking at paintball and scuba diving.
A paintball gun powered by a CO2 cylinder (positioned under the shooter’s arm) experiences 894 psi at an ambient temperature of 75ºF. No one is worried the paintball gun’s CO2 cylinder is too dangerous. In fact, some newer model paintball guns are powered by high-pressure air or nitrogen – between 3,000 and 4,500 psi.
A compressed air tank resting behind the head of a scuba diver can have pressure ranging anywhere from 2,400 to 3,500 psi. Again, no one says these pressure levels are dangerously high.
The Reality
The pressure in a CO2 system located inside a grocery store is actually lower than the pressure used to power paintball guns and scuba tanks, and we don’t think twice about playing paintball or scuba diving.
Myth 6: Leak Rates in CO2 Systems Are Greater Than 100%
This myth needs some clarification of terms. There is a difference between leak rates and emission rates. Leaks can occur in any system and, if left undetected, can go unnoticed for days, months or years. This releases a large rate of fugitive gases into the atmosphere. Emission rates, on the other hand, concern three areas:
- Actual leaks in piping or fittings
- Service and repair activities in which gases may need to be vented to the atmosphere
- Power failures that force the relief valve to open and emit gases into the atmosphere
As a real-world example, a system for a food retailer holds approximately 400 pounds of CO2 total. When surveyed, a contractor said he adds approximately one 40-pound cylinder per year, which is a leak rate of 10% – nowhere near 100%.
To demonstrate emissions due to a power failure, Hillphoenix tested a system with a 650-psi (45 bar) relief valve on a CO2 system’s suction line. When the system was shut down, the 650-psi relief valve activated after 7.5 hours.
An added benefit of CO2 is that it’s odorless, non-corrosive, non-toxic and non-flammable. That means there’s no reclamation system needed.
The Reality
You must differentiate between “leak rate” and “emission rate.” When you do, it becomes apparent that a typical leak rate for a CO2 system is closer to 10%. And if emissions occur during service or repair, there is no need for a reclamation system.
Myth 7: Refrigerant-Grade CO2 Isn’t Widely Available in North America
In 2020 and 2021, outside factors contributed to this myth – contaminated wells and a shortage of CO2 cylinders chief among them. There were also notorious supply chain issues.
But CO2 supply worries are essentially a thing of the past.
For many years, refrigerant systems required 99.99% pure Grade 4 Coleman/Instrument-Grade CO2. This level of purity was needed to ensure that the CO2 did not contain excessive impurities or moisture.
However, there has been a change in the grades of CO2 approved for use in refrigerant systems. A regulation change now allows 99.9% pure Refrigerant-Grade CO2 to be used as it has comparable purity and moisture levels.
Also, in cases of emergency or a shortage of higher-grade CO2, lesser grades may be used as long as the following precautions are taken:
- A filter dryer is used during charging activities.
- The user verifies that no air or non-condensable gases are present in the CO2 after charging.
The Reality
Refrigerant-grade CO2 is widely available from many suppliers in North America, and both Refrigerant- and Coleman-grade CO2 are now acceptable for refrigeration systems.
Myth 8: Adiabatic Gas Coolers Are Required in Warm Climates and They Use Too Much Water
Operators have used adiabatic gas coolers for years to keep system pressures lower and save on energy costs. Adiabatic gas coolers must be used in regions where the ambient temperature can reach or exceed 101ºF, according to the American Society of Heating, Refrigeration and Air-Conditioning Engineers (ASHRAE).
ASHRAE operates 2,943 climate stations in the U.S. and Canada. Only 14% (roughly 410 sites) of these climate stations – most of which are in the western U.S. and Canada – experience 101ºF ambient temperatures.
There are also cherry-picked examples, like a store in a hot southwest climate that uses a lot of water. What they don’t tell you, though, is that the facility is massive – three times the size of a typical store.
And if an adiabatic gas cooler is operated in a normal-sized store and in a higher water-saving mode, significantly less water will be used.
Other methods to keep operating pressures low during hot summer days are utilized worldwide and are currently being field trialed in North America.
The Reality
Those who argue adiabatic gas coolers must be used in warmer climates – and that they are simultaneously water hogs – are being selective with the data and not telling the entire story.
Myth 9: CO2 Transcritical Systems with Dry Gas Coolers Require Water Spray During High Ambient-Temperature Conditions
Some people are convinced that a sprinkler is needed on a system with a dry-gas cooler to keep the system pressure low when the ambient design temperature gets close to 100ºF.
To refute this myth, data was gathered from many refrigeration installations with dry-gas coolers in the Upper Midwest. Even as the ambient temperature approached 101ºF, the dry-gas cooler continued to operate as expected.
There was no need for a sprinkler.
Even at that elevated temperature, the high-pressure valve never came close to fully opening.
The Reality
A properly sized and maintained dry-gas cooler does not require water spray as ambient temperatures rise toward 101ºF.
About the Author
Scott Martin is the Senior Director of Industry Relations and Compliance at Hillphoenix, part of Dover Food Retail.
He earned his mechanical engineering degree from Southern Polytechnic State University and has more than 40 years of experience in the refrigeration industry.
He can be reached at smartin@doverfoodretail.com.