Utility Incentives: Lack of standard industry benchmarks still a challenge
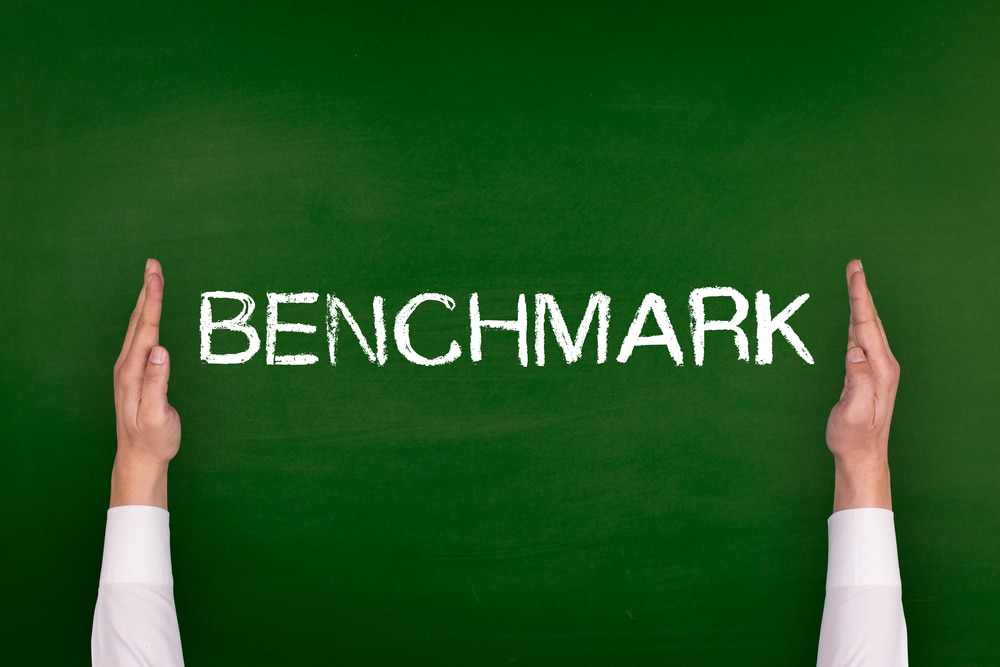
If you’re going to reward improvement, you need a baseline against which to measure it. Therein lies one of the many challenges facing refrigeration end-users seeking utility incentives for upgrades and new installations. As utilities, manufacturers and end-users work together to make newer, more energy efficient equipment more affordable through incentives, the lack of standard industry benchmarks makes the process complicated, fragmented and inconsistent.
Manufacturer calculations are apples and oranges
Within the refrigeration manufacturing industry, there is no uniform energy performance baseline for either CO2 or DX systems. Each manufacturer has its own set of tools for calculating energy consumption, and most of them only account for compressor energy consumption, ignoring other system components such as condenser fans and VFDs. Utility incentives aside, the lack of uniform performance benchmarks makes it difficult for end users to compare equipment performance and make the most informed purchase decisions.
Even within the utility industry, there is no agreed-upon calculation methodology. When utilities want to provide end-user incentives for new, more energy-saving equipment, they often use a set of measures that is entirely unique to that utility and that utility alone. One of the great barriers to uniformity among utilities is the lack of information sharing that goes on among utilities.
Utilities lack experience with natural refrigerant systems
Further complicating matters is the move toward natural refrigerant-based systems. Natural refrigerants are so new that many utilities have little or no experience with the technology and therefore make assumptions about how natural systems compare to traditional DX systems. Those assumptions are usually wrong. Most utilities also fail to give credit for the prevention of refrigerant leaks, even though a system that is not running on a full charge will use more energy to get the job done. Convincing utilities to recognize the dollar value of safeguarding energy efficiency through leak-avoidance is a tough sell, so it’s rarely accounted for in energy calculations.
The establishment of a baseline gets even more complicated when you begin looking at the different types of scenarios in which new, more energy efficient equipment might be installed, such as a full retrofit, a partial retrofit or a new store installation. The absence of an agreed upon set of energy benchmarks results in wildly varying incentives from one region to another. And it means that end-users have to reinvent the wheel every time they approach a new utility with a request for incentives.
Until industry stakeholders (manufacturers, utilities and end-users) agree upon a set of baseline standards for measuring energy efficiency, the best way for stores to secure incentives is to partner with an industry expert who can both manage projects and work directly with utilities. This approach not only relieves stores of the burden of going after incentives, but it also makes for better coordination of projects that involve multiple utility companies — and potentially varying baseline measures.